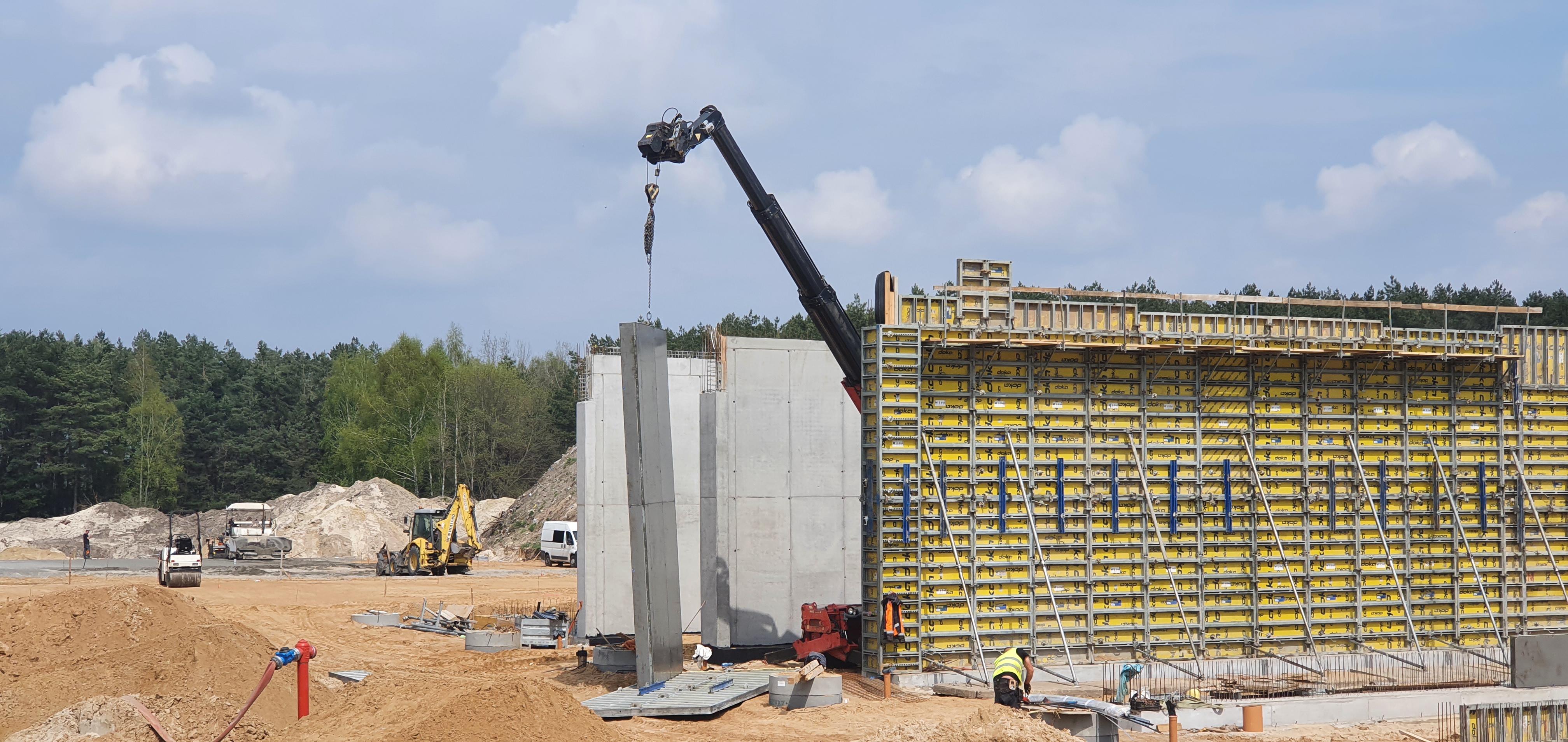
Commissioning is usually understood as the electrical, mechanical and technological (performance, quality, etc.) commissioning of the installation.
In accordance with the above-mentioned provisions, mechanical-electrical and technological commissioning is most often referred to (according to FIDIC - "Final Trials" and "Operational Trials"). In order to perform commissioning, it is necessary to have documentation of the installation/equipment and all tests referred to in the construction law, health and safety and fire regulations and other regulations in force in the country in which the installation will operate.
This type of commissioning/testing includes safety and fire training, job training and work on the plant
The person in charge of commissioning, "Technologist" or "Commissioning Specialist", during the operation of the plant notifies the crew of the responsibilities, keeps them informed and shows the results of the work. The knowledge gained at the various positions is to contribute in general to the effect imposed on the installation, i.e. to achieve, first of all, the efficiency and quality of segregation in accordance with the market requirements for the product (quantity, degree of contamination) . In the implementation of this process, special attention should be paid to ensure that the load on the plant is gradual - this will enable newly hired employees to perform their duties effectively and with understanding.
If not specified by the Employer, the start-up/test documentation shall include :
For the purpose of a full, independent assessment of the correctness of the implementation of the investment in terms of its scope, quality and purpose, as well as the achievement of the planned technical and technological parameters, it is necessary to carry out Operational Trials
Operational tests are carried out under the conditions of current operation of the project (plant operation under load) for min. 3 months - a representative time period, allowing to collect data for:
- to perform detailed analyses of the flow of waste streams, taking into account the division into individual process lines,
- to create correlations between the morphology of waste, the flow of individual waste streams and the specifics of the period of implementation of operational trials).
Supervision of the performance tests is carried out by a Commission consisting of:
- Representative of the Employer,
- Contractor,
- other persons appointed to participate in the tests by the Employer.
Among other things, carrying out operational tests gives the opportunity to identify possible defects and faults and report them during the warranty period, while the Final Report from operational tests provides valuable source material for post-implementation analysis that allows final settlement of the contract (investments subsidized by EU funds).